The European fabric and textile industry is going through rough times. Faced with increasing global competition, a lack of flexibility, supply chain disruptions, and rising costs, it’s do or die for textile manufacturers.
Here’s how open digital technologies can help overcome these challenges, so production companies can not only survive, but also thrive in a tough industry.
Top challenges for the textile & fabric industry
The textile and fabric industry isn’t for the faint of heart, faced with several specific challenges that threaten both its current operations and future viability.
Suboptimal delivery reliability and flexibility challenges
One of the most significant challenges in the European textile industry today is maintaining delivery reliability while adapting to smaller, more varied orders. With the market moving towards customisation and reduced lot sizes, textile manufacturers are under immense pressure to be both flexible and efficient.
However, many production environments are hampered by outdated machinery and production processes that are not designed for quick order and process adjustments. This often leads to inefficiencies caused by last-minute schedule changes, longer production lead times, and increased operational costs, all of which undermine delivery reliability.
The need for market differentiation
European textile manufacturers are particularly hard-hit by competition from countries like China, Turkey, and Bangladesh, where lower production costs allow for aggressive pricing strategies. As an EU manufacturer, competing on price alone is not sustainable. Instead, companies must differentiate themselves through innovation, quality, and flexibility.
This shift requires more than just improved production techniques: it demands a complete rethinking of how data is used across the organisation to drive smarter, more agile operations.
Impact of supply chain disruptions
Supply chain disruptions driven by factors such as geopolitical tensions, have caused significant volatility in the availability and cost of raw materials like cotton, linen, and polyester. This unpredictability affects not only the cost of production but also the ability to maintain consistent production schedules. The ripple effects are felt throughout the industry, impacting everything from the initial production stages to the final retail prices of textile products.
Inflation and soaring energy prices
The textile industry is also grappling with the pressures of inflation and rising energy costs. Energy-intensive production processes mean that even small increases in energy prices can have a significant impact on overall costs.
At the same time, there is increasing pressure to meet stringent sustainability standards, which adds another layer of complexity to already thin profit margins. Manufacturers must find ways to reduce energy consumption and improve efficiency without compromising on quality or production capacity.
Slow adoption of digital technologies
Despite the clear advantages of digital transformation, the textile industry has been slow to adopt new technologies.
This reluctance is partly due to the capital-intensive nature of textile machinery, which is built to last for decades. This leaves many manufacturers struggling with outdated systems that hinder real-time data visibility and operational efficiency.
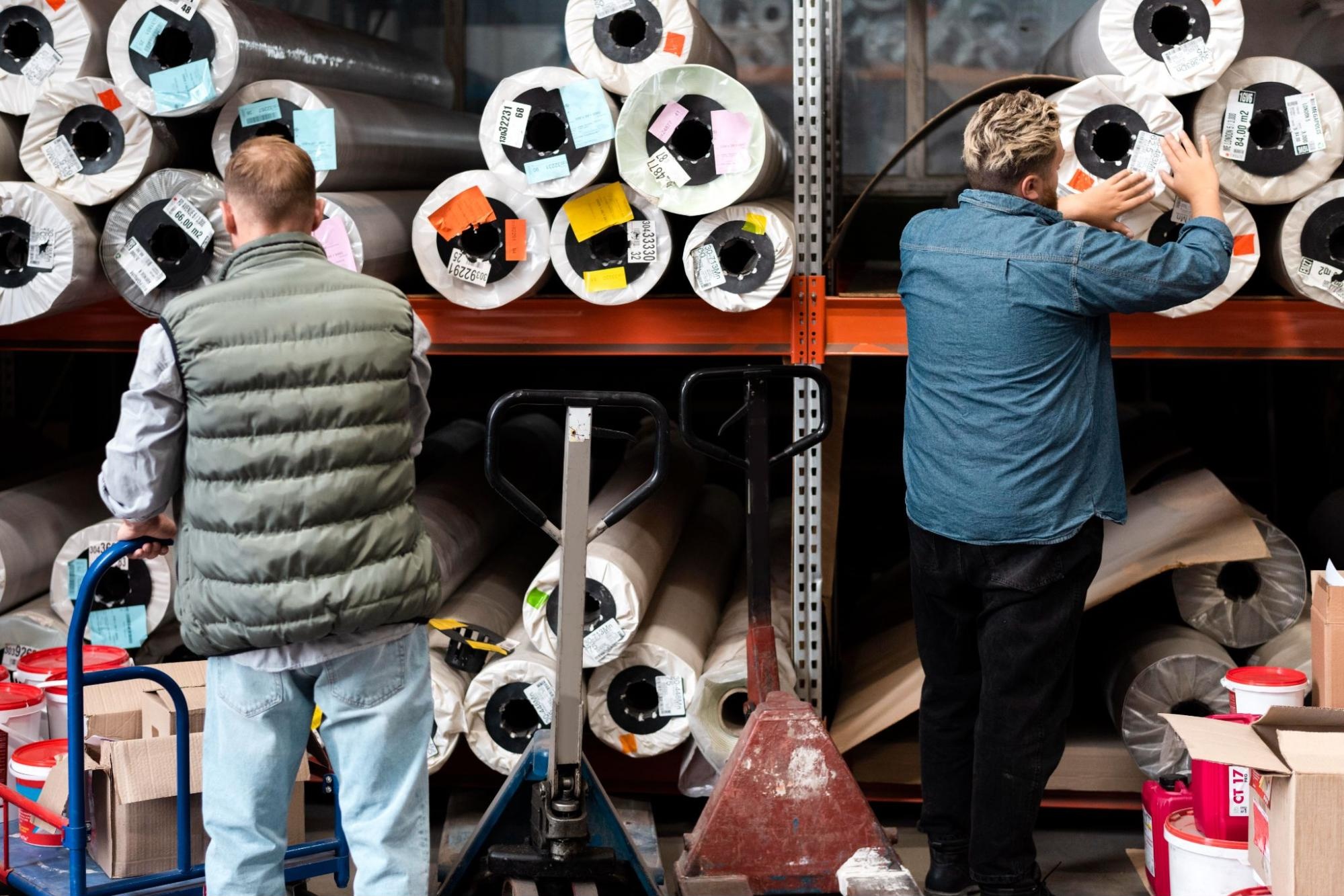
The path forward: embracing digital transformation with open technologies
For many, the answer to these challenges lies in digital transformation, but the path forward isn’t just about adopting technology as such.
To navigate these challenges, the textile industry must embrace digital transformation, but not just any digital transformation. The key lies in adopting open, scalable, and cost-effective technologies that offer a modular approach to manufacturing execution systems (MES).
Unlike traditional MES solutions, which can be rigid and costly, open technologies provide the flexibility needed to adapt quickly to changing market demands. This modularity allows manufacturers to implement only the features they need, scaling up as necessary without incurring prohibitive costs.
Why open technologies matter
Open technologies offer several critical advantages over traditional MES systems. First, they are inherently more flexible, allowing manufacturers to customise their systems to meet specific operational needs. This flexibility is crucial in an industry where requirements can change rapidly due to shifting market demands. Additionally, open technologies are often more cost-effective because they avoid the pay-per-use pricing models common in proprietary systems.
This makes it easier for SMEs in the textile industry to adopt advanced technologies without breaking the bank.
The benefits of a modular approach
A modular MES system allows you to build your digital infrastructure step by step, implementing only the functionalities you need at any given time. This approach reduces upfront costs, ensures that the system can evolve alongside your business, and creates buy-in.
For example, you may start by implementing real-time production monitoring and order management and later add advanced features such as waste and defect management, material management, or OEE as your needs grow.
This adaptability is essential in an industry where the ability to respond quickly to market changes can be a significant competitive advantage.
FactryOS: a perfect fit for the textile industry
In the context of textile and fabric production, FactryOS emerges as an ideal solution for manufacturers seeking to modernise their operations.
FactryOS is a modular, web-based MES system designed to provide end-to-end data visibility and streamline production processes. Its open architecture and flexible modules make it uniquely suited to the needs of the textile industry, offering a range of features that can be tailored to specific operational requirements.
Key features of FactryOS
- Establish lean production operations: FactryOS helps you streamline your processes, reduce waste and optimise inventory and work-in-progress (WIP) levels.
- Gain end-to-end data visibility: With real-time dashboards and tailored KPI reports, FactryOS provides operators and managers with the insights they need to reduce downtime, waste, and bottlenecks.
- Follow up on the status of orders or batches: Accessible from any device, FactryOS allows managers to monitor the progress of orders and batches in real-time, ensuring timely adjustments as needed.
- Adapt production on-the-go: The system’s modular nature enables manufacturers to flexibly adjust operations to meet evolving customer demands, enhancing agility and responsiveness.
- Avoid unplanned downtime: By identifying trends and bottlenecks before they cause downtime, FactryOS helps maintain continuous production and improve overall efficiency.
- Radically Reduce Waste: In-process quality checks and real-time data capture help eradicate reworks and scrap, contributing to a leaner, more efficient production environment.
- Get a global view on operations: FactryOS allows manufacturers to compare the performance of multiple lines and sites at a glance, providing a comprehensive overview of operations.
Use cases: How Helioscreen and Copaco increased their flexibility and profit margins
Eager to see what that looks like in practice? Here’s the story of how two textile producers leveraged open technologies to make their production more efficient, resulting in increased operational efficiency and profitability.
Copaco Screenweavers (sunscreen fabrics)
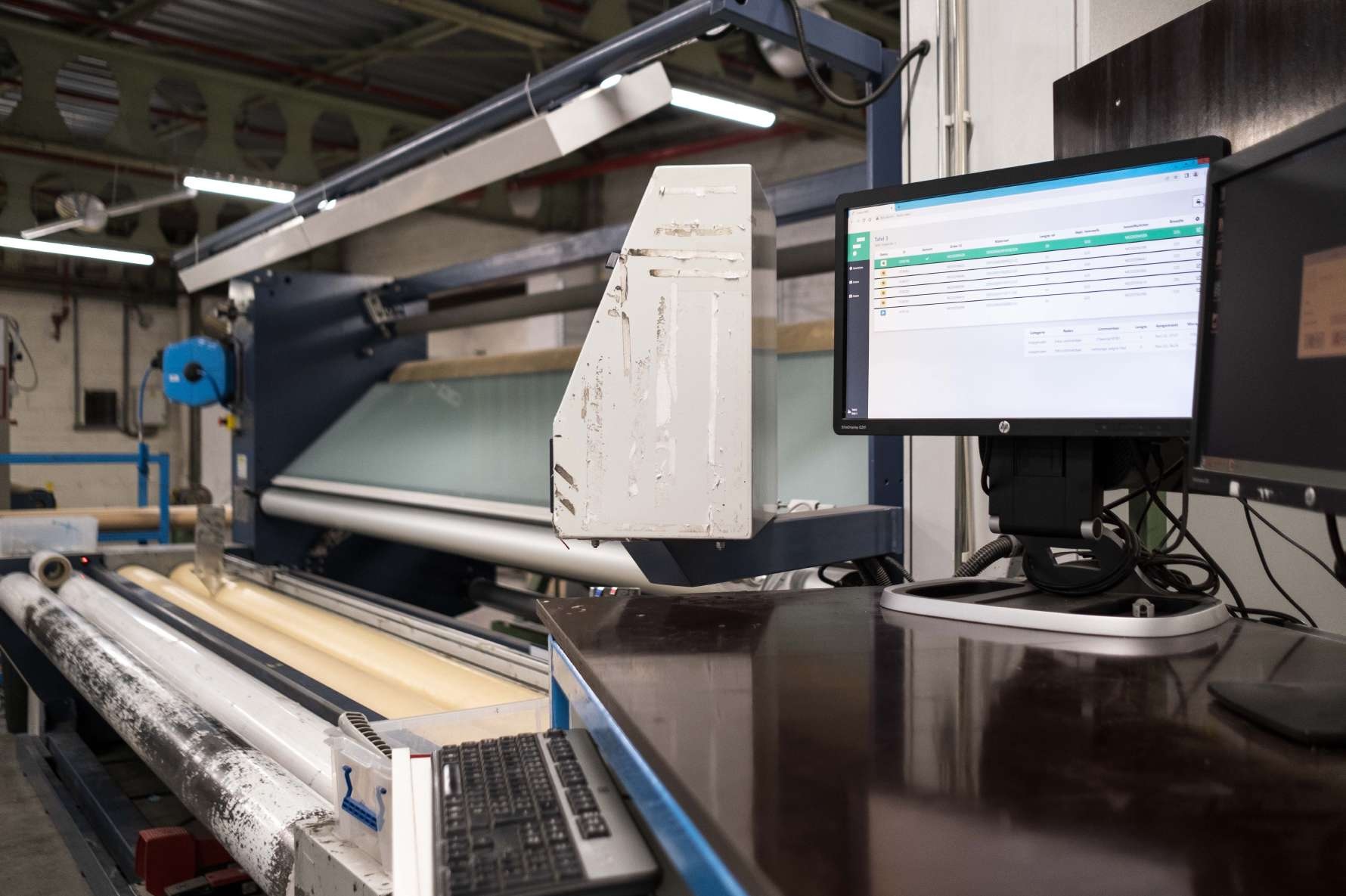
Copaco Screenweavers, a leading producer of sunscreen fabrics, struggled with the limitations of paper-based workflows that restricted real-time visibility into their manufacturing processes.
By implementing FactryOS, they transitioned to a digital manufacturing system, allowing for immediate insights into production efficiency, yield, and material usage. This shift has not only streamlined production planning but also significantly reduced waste and improved Overall Equipment Effectiveness (OEE), resulting in more precise and agile manufacturing operations.
Before implementing FactryOS, we lacked real-time process visibility. Because we only sign off a production order at the end of the process, we had little overview of work in progress. Now, we have an accurate picture of current orders and their statuses at all times. That’s a gigantic improvement. - Andy Vanderpoorten
Helioscreen Fabrics (sun protection materials)
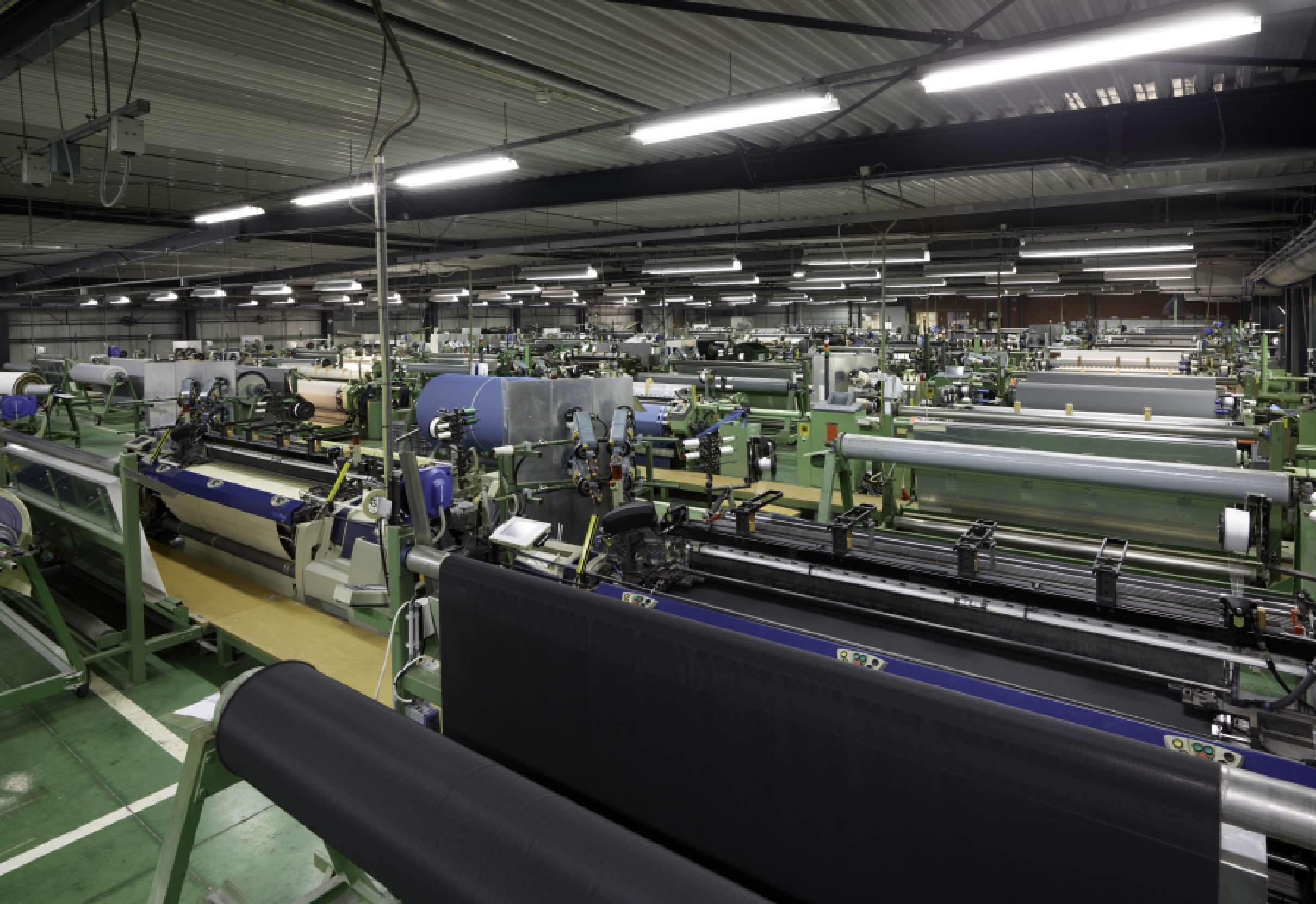
Helioscreen Fabrics, known for its high-quality fibreglass sun protection fabrics, aimed to create a more responsive and efficient production environment.
By implementing FactryOS, they were able to eliminate paper-based processes and gain real-time visibility into their operations. This allowed Helioscreen to optimise machine utilisation, reduce downtime by 65%, and enhance overall production efficiency, helping them meet the increasing demands of a competitive global market.
FactryOS now gives operators the right information at the right time through user-friendly screens. A clear sign of our factory’s improved efficiency is the fact that the planning parameters we used before no longer match reality. - Stefaan Claeys
To sum it up
By embracing open, scalable, and modular solutions like FactryOS, textile manufacturers can overcome the challenges of flexibility, efficiency, and global competition. Our MES platform provides the real-time insights and operational agility needed to thrive in today’s complex market environment, positioning your company for long-term success and innovation in many years to come.