Harnessing FactryOS, ice cream manufacturer Jacques IJs replaced its paper-based processes with a digital production workflow. The results: overall efficiency gains, cost savings and increased yield. Find out how the MES has also radically improved the workflow of machine operators on the floor.
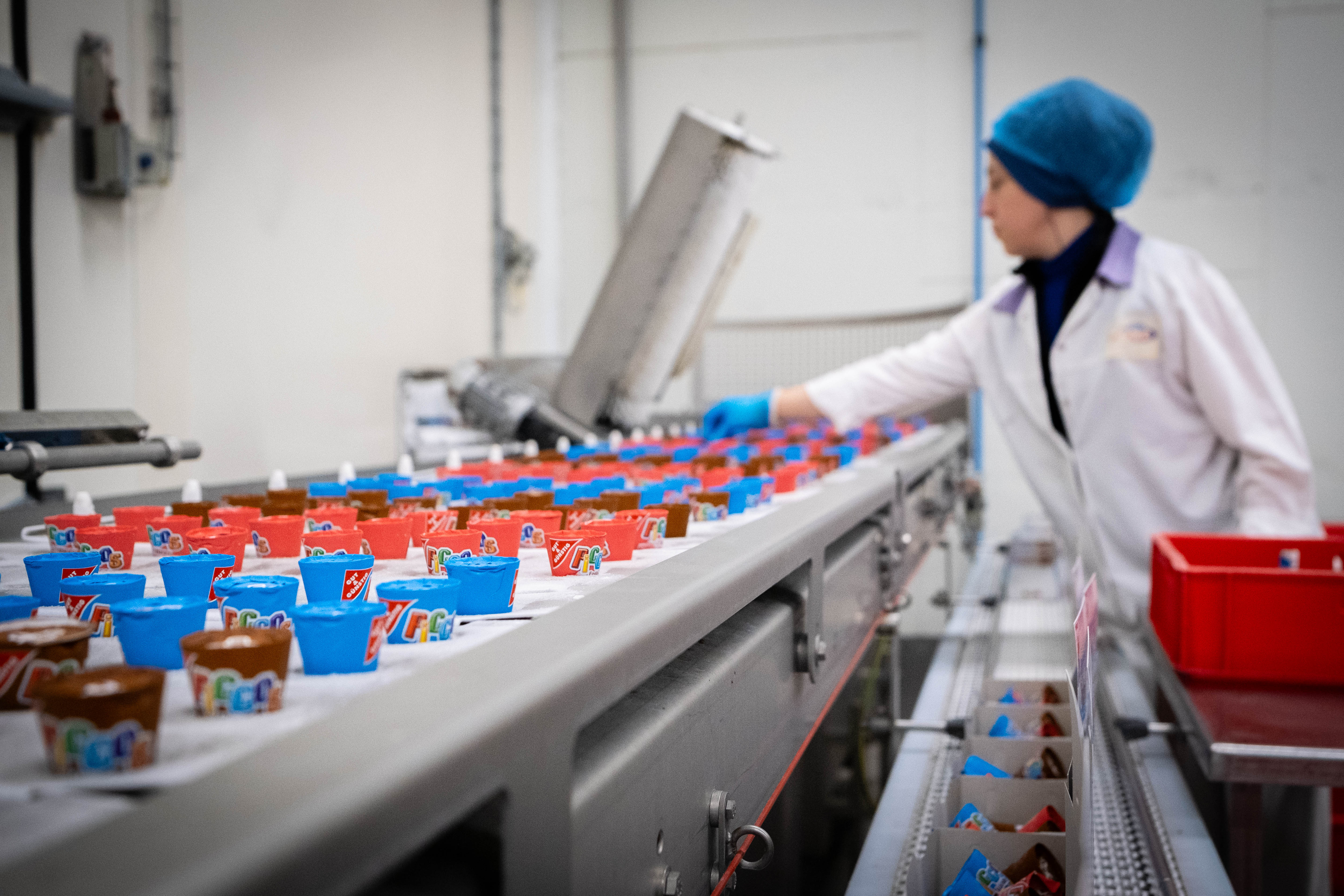
People matter to Jacques IJs.
That's why the Belgian ice cream supplier wanted to improve the working experience of their employees, and finally digitise its manufacturing operations. Their weapon of choice: our modular MES platform FactryOS.
How are operators perceiving their newfound digital workflow? How smoothly did the adoption process go? And what are the returns on investment the company is witnessing today?
We spoke with the company's IT manager and Production Planner, two of the leading forces behind the company's ongoing digitisation efforts. “Our machine operators really love working with the MES. And that was the whole point.”
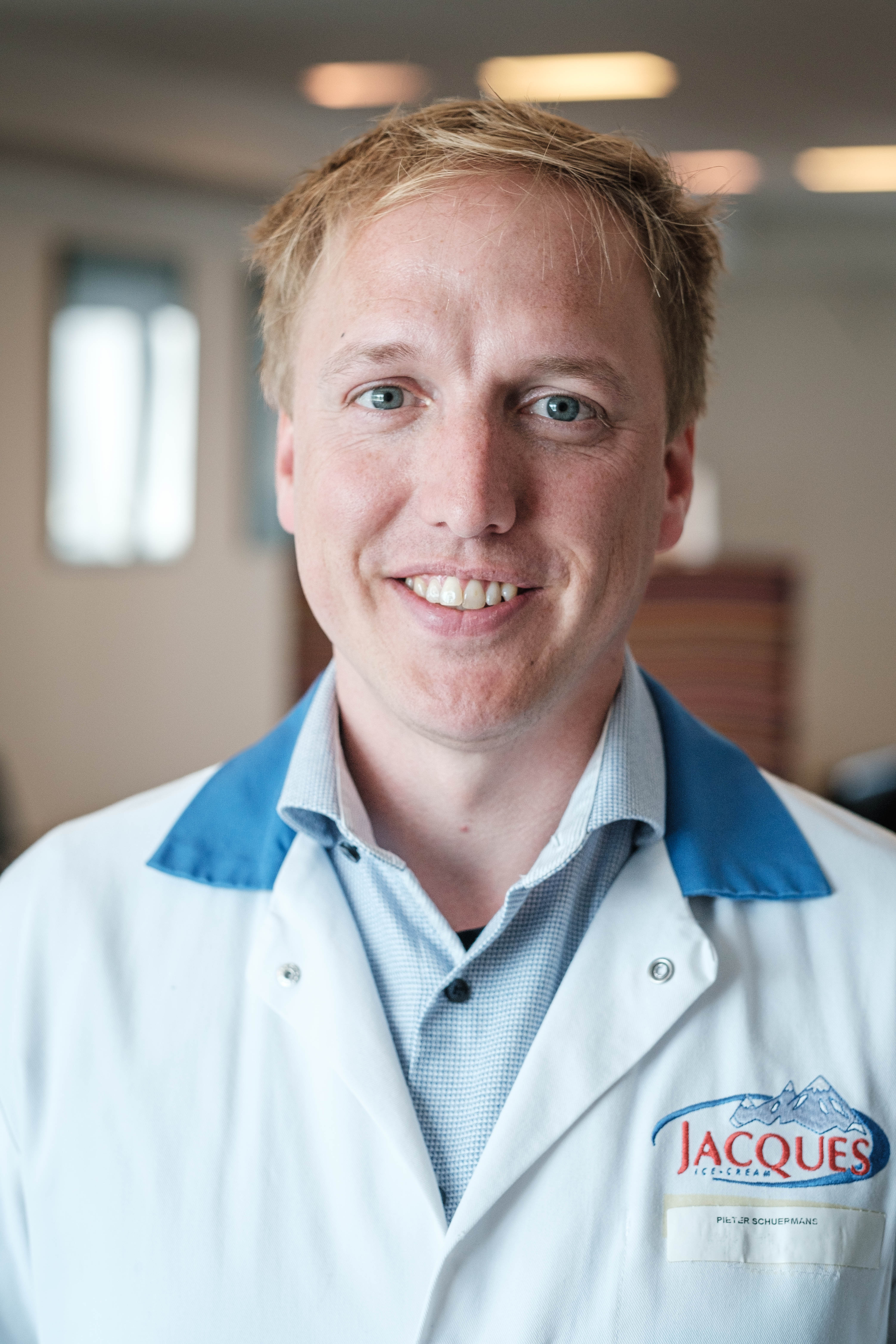
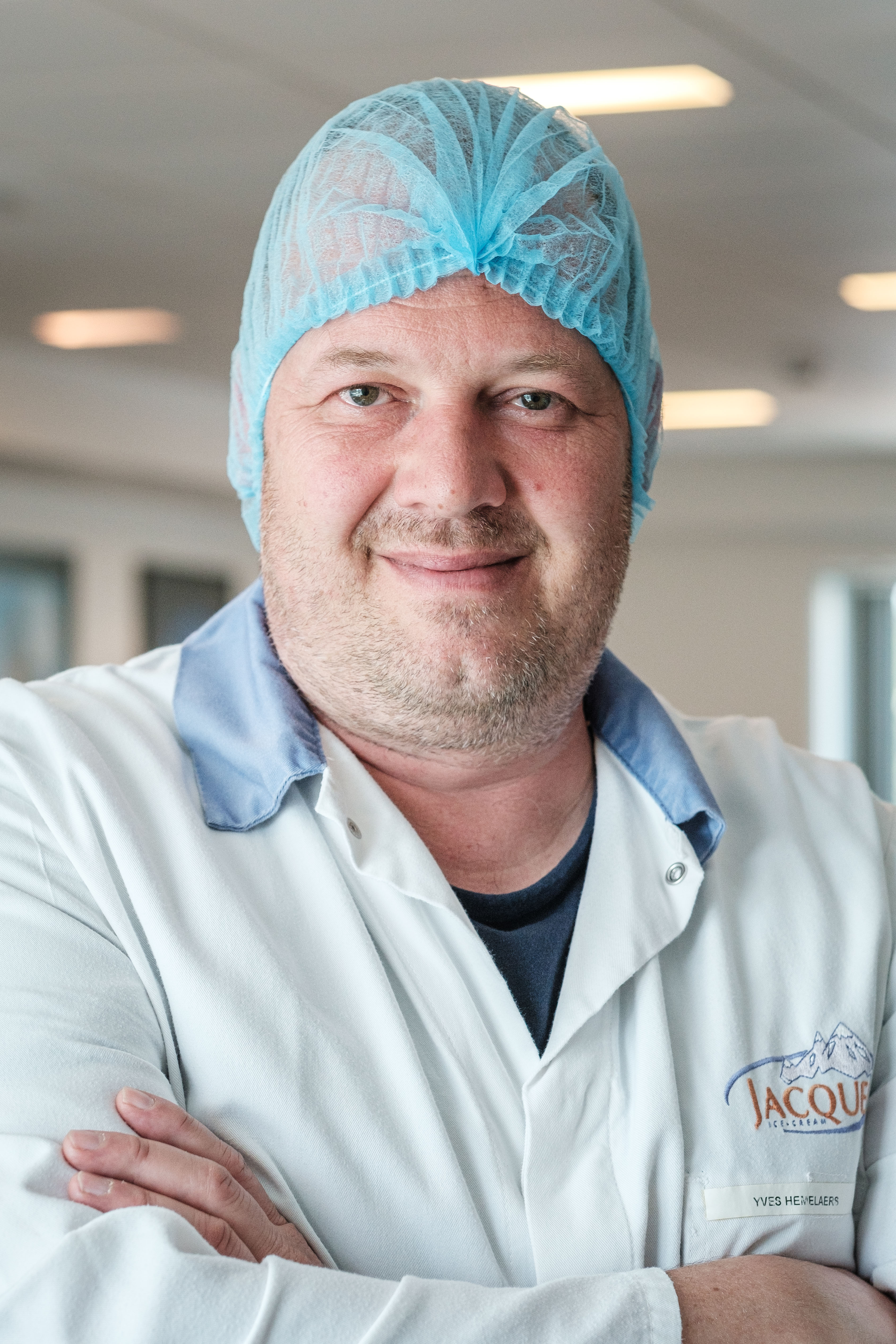
Interview: shaping digital transformation in manufacturing
"Manufacturing is not quite the standard IT environment", says IT manager Pieter Schuermans. "It involves a lot of technical challenges and networking. And it's simply fun to be on the production floor, instead of sitting behind a desk", he smiles. Alongside him is Production Planner Yves Hemelaers.
Over the years, his role in the company has changed a few times, going from Team Leader, to Production Coordinator, and now Planner. "As a Coordinator, I once developed our first data analysis initiatives", Yves says. "Today, I make sure that sales orders are correctly planned and executed in production."
Why did you decide to implement an MES in the first place?
Yves: "We were really struggling with a paper-based workflow . On every production run, operators had to manually fill in a series of checklists on paper, which was prone to errors. This also made it impossible to investigate the data in real-time, and to intervene quickly in case of process deviations."
Pieter: "Our number one priority was to create a paperless factory , aiming to modernise production operations and obtain a technological edge on our competitors. At the same time, we wanted to offer our employees a better working experience , by offering them a visual, and user-friendly interface."
Why FactryOS and not another MES platform?
Pieter: "A crucial point for us was that it is a highly intuitive MES platform. After scanning the market, we found that FactryOS was the most user-friendly option. And while most other solutions lacked the flexibility to meet our variable processes, FactryOS could be completely adapted to our needs ."
Yves: "Solutions from other vendors were a lot more rigid, which often meant: take it or leave it. Some things weren't possible, or we couldn't shape it to our specific requirements. This was crucial to us, as we wanted the tool to be adopted well by our operators, which is key to achieving lasting change."
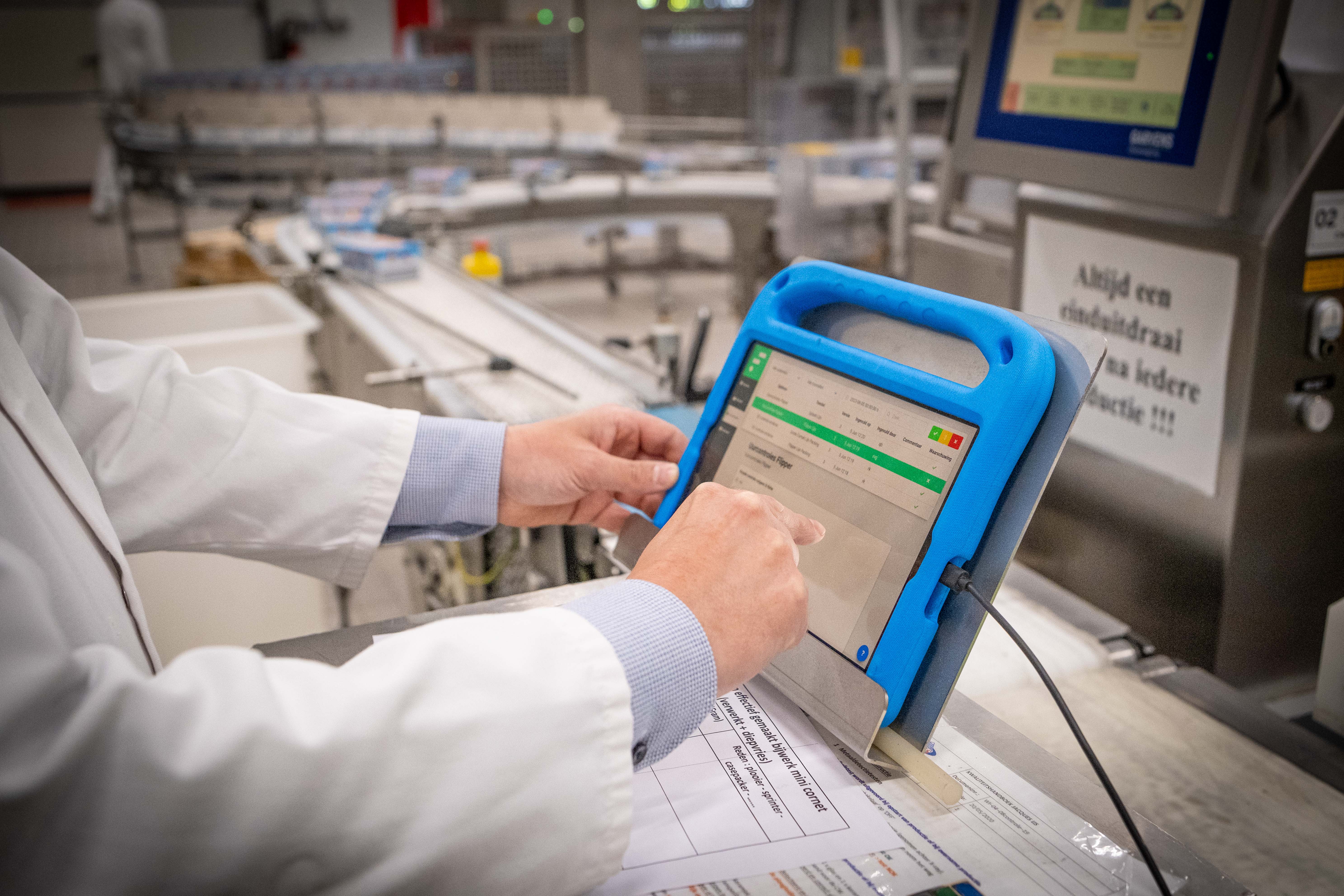
How has the MES software changed the lives of operators?
Pieter: "For each production run, about 500 pages were printed, going from process cards to weighing forms. This paper overload would often cause confusion, and unplanned downtime. By removing paper, machine operators are now able to focus on the things that matter most, and do their jobs better."
Yves: "We see that production is now running smoother and with less stress. Having a tablet available at each production station, has brought more peace of mind to the floor. No more tangled papers, no more missing documents, all relevant information is now visible on the device and immediately accessible ."
How did the operators respond to a new way of working?
Pieter: "Implementing the MES implied a huge change for them, while digitisation isn't easy for everyone. Nonetheless, machine operators consider the tool as a great improvement to their working environment. They're really convinced of the added value the software brings to their day-to-day jobs ."
Yves: "The visual interface was well received by our employees. After only a few training sessions, they were able to use it. Today, we are still getting lots of positive feedback , which proves it has made their lives easier. People are genuinely happy to work with the software. And that was the whole point."
How did you ensure a rapid user adoption?
Pieter: “At the start of the project, we tested out many visual components, to make sure we were heading in the right direction. Factry updates were quickly shared and reviewed by a panel of key users. In this way, we could make important adjustments early on . As a result, the adoption went smoothly.”
'For digital transformation to be successful in the long run, it is important to demonstrate operators the benefits, and the problems it solves for them. Before implementation, we have set up a demo to show them how it works. And whenever a new functionality is added, we light out the possibilities.”
Yves: "Even today, operators keep being involved in improving the user interface . This often results in small improvements, such as adding a certain button or integration."
How has the software impacted the IT department?
Pieter: "It's a new way of working, for sure. Before, I had to read out Excel files and connect them, to make sure that the right data got printed. It was quite a cumbersome solution, while any IT department in fact aims to reduce the number of spreadsheets . FactryOS has helped us to finally do that."
And other departments, such as Quality or R&D?
Pieter: "For the quality department as well, it's quite an improvement to be able to retrieve any type of information digitally, instead of having to dive deep in boxes of paper. In case of quality anomalies, they can now intervene much faster because they are notified instantly, and not 24 hours later."
Yves: "Also, lab technicians were able to build an additional safety hurdle into the production process. Whereas with paper processes, operators could theoretically start the process before the lab had verified the order and cleared the line. Now, the line is automatically blocked until every check is completed."
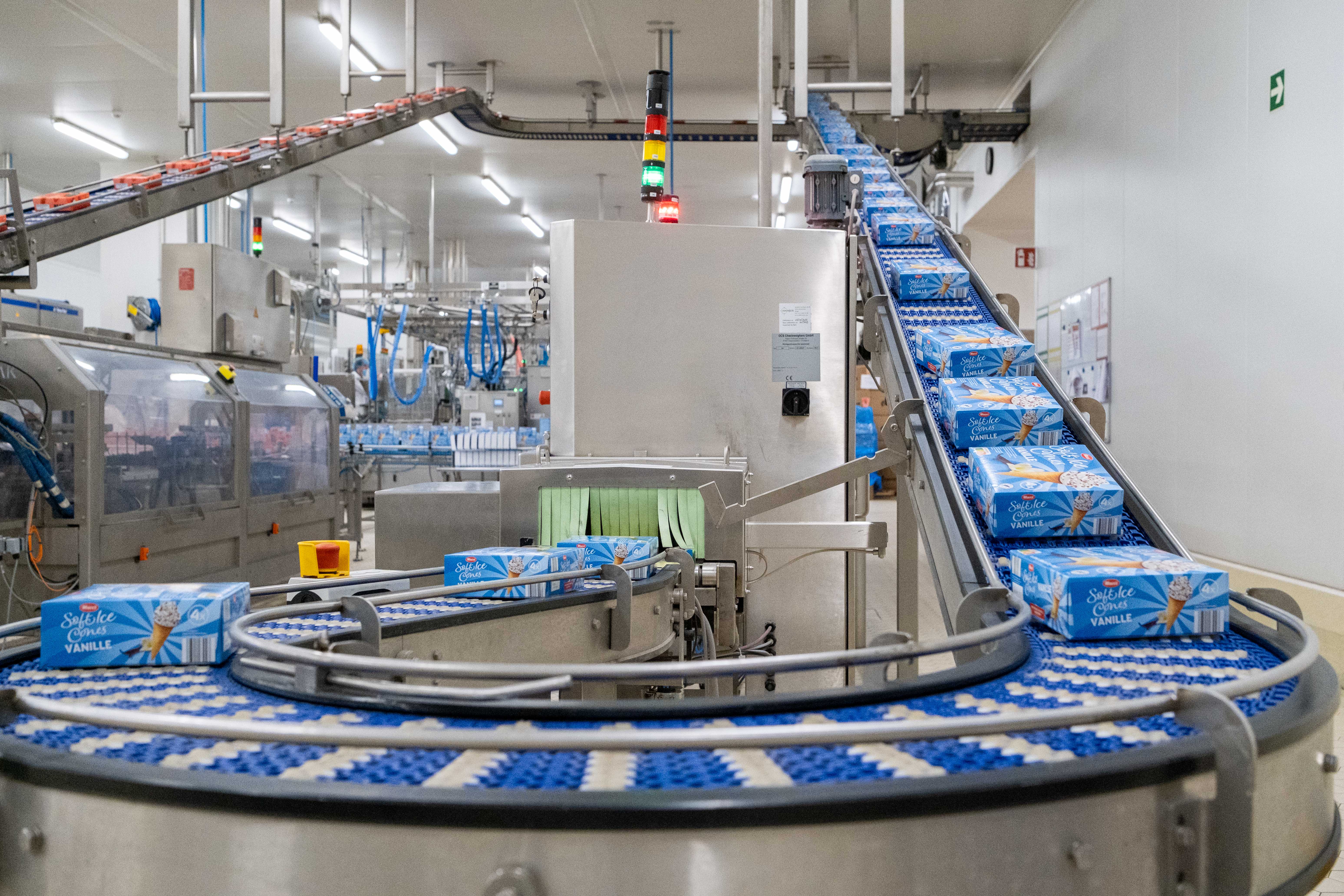
Has it also improved collaboration between departments?
Yves: "Before FactryOS, I had to make a lot of phone calls. Now there is a single source of information to check up on the status of production, or to prepare a meeting. So yes, it has brought more coherence to the collaboration between the quality, planning, and production team, and the management ."
What other returns-on-investment are you noticing today?
Yves: "Decreased downtime, for instance, because production isn't stopped anymore due to wrong or missing papers, or issues with wrong lot numbers. We're not measuring Overall Equipment Efficiency (OEE) on all lines yet. However, I calculated it for one of them already, and it has improved by 10%."
"Also, due to real-time monitoring through the MES, our product overfill has decreased by 15 to 20%. This means we can now e.g. produce 100 items instead of 85 with the same amount of raw materials. When you're producing an amount of 235 million ice creams a year, that makes a huge difference."
"Despite the fact that we are producing more than last year, we are clearly noticing a downwards trend in customer complaints. At the same time, the tool has improved our traceability. In case clients have a question, we can now send them any data they need in every stage of the production process."
How do you plan to continue enhancing the operator experience?
Pieter: "At this point, we're focusing on fine-tuning the MES system, before we connect the final lines. Later this year, we're looking at a number of new improvement projects. For instance, we are planning to automate downtime management, relieving the operator from assigning the reasons for stoppages."
Yves: "To add more production context, we're also planning to implement real-time dashboards on the production lines, so operators can follow up on different aspects of the process, such as waste and energy consumption. We're excited to further collaborate with Factry on these new initiatives."